RISD Rover
RISD Rover is a student team at the Rhode Island School of Design that competes in NASA’s annual Human Exploration Rover Challenge. The team spends 9 months designing, prototyping, analyzing, and fabricating a human powered vehicle that must traverse a Mars-like obstacle course. The 2 riders must perform tasks such as sample collection and instrument deployment on the course as well. The race takes place at the Marshall Space Flight Center every Spring.
I spent 3 years on the team, 2 of those years as a team leader. I primarily did work on the composites systems; wheels, seats, and suspension. Other contributions included brazing, machining, sewing, overseeing physical fitness training, and riding the rover at competition. In addition to design and fabrication work, I organized the team and taught new members relevant skills.
Process
For each system, we began by creating CAD models and small physical prototypes that we could test either physically or digitally, using Finite Element Analysis (FEA). For carbon fiber components, it is difficult to conduct FEA due to the nature of the material, so we relied on small scale models and physical tests to determine stress points and edit the design. Every year, our designs evolved and iterated on previous knowledge. We analyzed failures from previous races and drew on existing examples from the real world to achieve strength, flexibility, and weight reduction where appropriate.
Team leaders held demos in skills such as brazing, welding, mold making, and carbon-fiber fabrication to engage and educate new club members in how to make components for the rover. This allowed new members to learn from more experienced team members and learn skills that are not taught anywhere else at the Rhode Island School of Design.
In addition to design and fabrication, the team also conducts STEAM outreach to local schools and events.
The team sold t-shirts and patches to help fund travel expenses.
The rover consists of multiple subsystems, each led and coordinated by various team leaders. These systems must combine smoothly to make a properly functioning vehicle.
Carbon fiber fabrication using an “infusion” layup process
We tested ergonomics and seat spacing by building a jig on which riders could sit and pedal.
Wheel and Tread testing and iteration 2016-2019

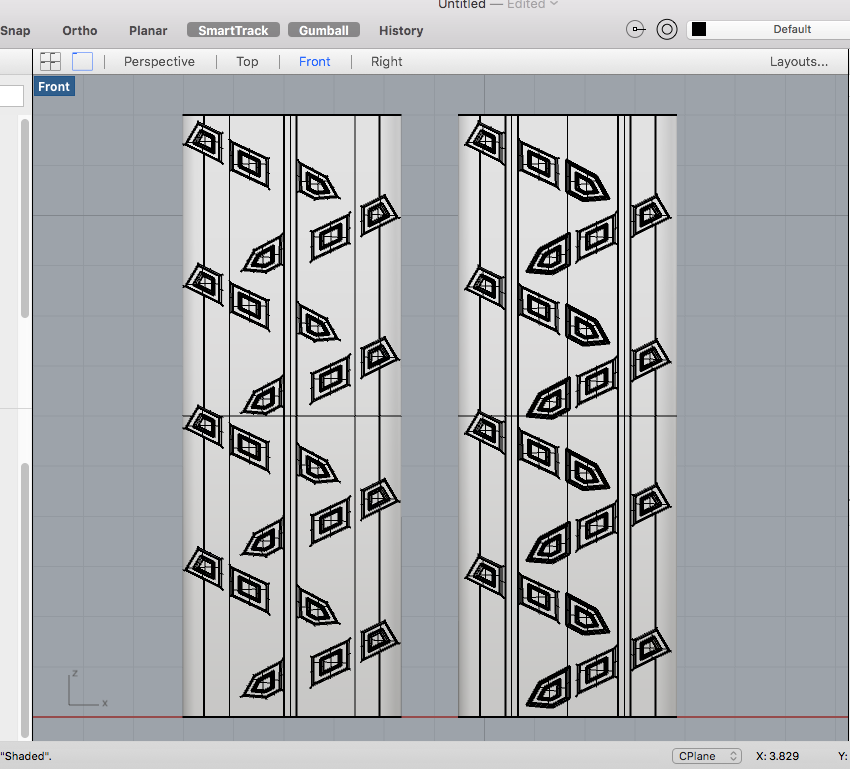
The chassis of the rover consists of chromoly steel, and all joints were either brazed or welded, depending on the type of connection. All elements of the rover other than the bike components and some chassis tube bends were fabricated in-house by the RISD Rover team.
Final Product
The competition has certain requirements of all rovers; they must not have any pneumatic elements or any stored energy (such as batteries or flywheels), and they must fit into a 5 x 5’ cube at some point. Our solution to the size constraint was having the rover fold in half using a hinge and latch at the center of the chassis.
2018 seat front
2018 seat side
We always tested the rover on various terrains before going to the competition. This allowed us to see how the vehicle performed as a whole and gave us time to make adjustments before the race. These tests also allowed us to determine which team members were the fastest riders, and therefore who would pilot the rover during the competition.
In 2019 our vehicle was 88 lbs, the lightest in the history of this competition.
This gallery contains photos of the final versions of the rover from the 2017 to 2019 seasons. Both the 2018 and 2019 rover used the same chassis and differential, though the steering, suspension, and wheels of the 2019 rover are completely new. The 2017 rover can be recognized by its orange treads, the 2018 rover had upper and low A-arms with shock absorbers, and the 2019 rover had only upper A-arms and a carbon fiber leaf spring between the front wheels.

RISD Rover has done historically well at this challenge. In 2017 we won 2nd place, the Featherweight Award for Lightest Rover, Best Report Award, and the Technology Challenge Award for Best Wheel Design. In 2018 we received the Crash and Burn Award for resilience and problem solving in the face of adversity, and in 2019 we again took 2nd place and the Featherweight award.
RISD Rover 2016-2019
Team Advisor: Michael Lye